What is the manufacturing process of Portland Cement?
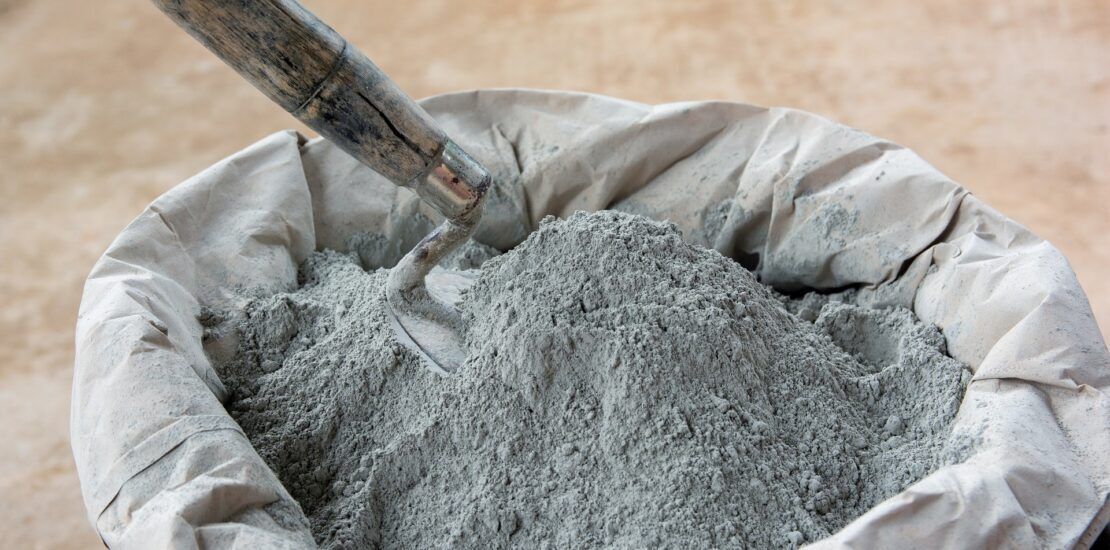
Portland cement is a fine powder made by heating limestone and clay minerals in a kiln and forms a clinker. The clinker is ground to a fine powder with the addition of a small number of other materials. It is the most commonly used type of cement in the world. It is a vital ingredient in concrete, mortar, stucco, etc. It is named Portland cement because of its similarity to Portland stone found on the Isle of Portland in Dorset, England.
Joseph Aspdin invented it in 1824. But the credit for the invention of the modern Portland cement belongs to his son William Aspdin in the 1840s.
What is Portland Cement made of?
Following mineral materials are used for the bulk and ongoing manufacturing and production of Portland Cement:
- Argillaceous material -CaCO3 < 40%, such as clay and shale.
- Calcareous materials -CaCO3 > 75% such as limestone, marl, and chalk.
- Blast furnace slag.
- Gypsum.
- Silica sand.
- Iron ore.
Cement factories are created where these raw materials are available in abundance and means for long-distance transporting raw and finished materials. The manufacture of Portland cement is a complicated process and done in the following steps:
1) Grind the raw materials.
2) Mix them in specific proportions based on their purity and composition, and
3) Burn them to sinter in a kiln at roughly 1350 to 1500 ⁰C.
During this process, these materials partly fuse to form nodular-shaped clinker by breaking chemical bonds of the raw materials and recombining them into new compounds.
The clinker is ground to a powder with the addition of about 3% of gypsum. The product formed through this process is Portland cement.
Types of Manufacturing of cement
There are two processes called “wet” and “dry” for cement manufacturing. One can choose either of them based on whether the grinding and mixing of raw materials are done in wet or dry conditions.
There is also a semi-dry process that differs from the above two processes. In this process, the raw materials are pulverized dry, mixed with about 10-14% of water, and burnt to a certain temperature.
The wet Process is prevalent in old age because of the possibility of more exact control in mixing raw materials. The deep mixing of raw materials in the form of powder was not available then.
The dry Process became widely used thereafter because of the modem development of dry mixing of powdered materials with the help of compressed air.
The dry Process demands much less fuel as the materials are already in a dry state, whereas the slurry contains about 35 – 50% water in the wet process. Let’s deep dive into both the Wet and Dry Processes in detail.
1. Wet Process
The newly quarried limestone is first crushed into smaller pieces in the wet process. Then in the ball or tube mill, it is mixed with clay with water to form a slurry. The slurry has about 35-50% water content, wherein particles crushed to the refinement are held in suspension.
After that, this slurry is pumped into slurry tanks. The limestone and clay particles are prevented from settling in the tank by blowing compressed air from the bottom of the slurry and are kept in ignited condition with the help of rotating arms with chains.
This slurry is held at the necessary chemical composition in a tube mill by testing and correcting from time to time and also tested in the different storage tanks by blending the slurry. After that, it is kept inhomogeneous in the final storage tanks by the slurry agitation.
A rotary kiln is one of the essential parts of the cement production plant. It is a 3m to 8m diameter steel cylinder lined with fire resistance refractory materials. It is fitted on roller bearings and can rotate about its axis at a scheduled speed.
When sprayed against a hot surface of a flexible chain, the slurry loses moisture and becomes flakes. These flakes peel off and drop on the floor. The rotation of the rotary kiln drives the flakes to move from the upper end to the lower end of the kiln, subjecting itself to more elevated temperatures.
The kiln is then fired from the lower end. Generally, the fuel used is powdered coal or natural gas for cement manufacturing. As the materials go ahead, the material rolls down to the lower end of the rotary kiln.
The dry material experiences a series of chemical reactions until about 20-30% of the materials get fused. Lime, alumina, and silica get recombined. It is where the oxides in raw materials will be united to form compounds in the clinker.
The fused mass turns into a nodular form of size three mm-20 mm, known as clinker. After that, the clinker is cooled in a rotary cooler. Then, cooled clinker ground in a ball mill. For the prevention of flash-setting of the cement, 3 to 5 % of gypsum is added. A ball mill is a hardened steel ball with different chambers charged in sequence forward.
The particles are powdered to the needed refinement level. And particles are divided by air currents and taken to storage. Then, supply it to the market as a final product and use it in various construction works such as Buildings and dams.
2. Dry Process
The raw materials are pulverized in a dry state in the dry and semi-dry processes. Then, they are processed in a grinding mill and made to very fine powder-like. The power is further blended, reworked for the suitable composition, and mixed with compressed air flow. A uniform mixture is obtained for nearly about one hour of aeration, and that aerated power tends to behave like a liquid.
Then, the blended meal is sieved and applied to process in a rotating disc called a granulator. About 12 percent by weight, a quantity of water is added to make the blended meal into pellets.
The blended meal is transformed into pellets by adding water, about 12% by weight. It is done to exchange heat by airflow during the further chemical reaction easily. Smaller equipment is used in dry Process compared to wet Process, and dry Process is also economical.
Nowadays, many cement factories use modern production technology to increase the capacity and quality of cement.
Modern technology uses equipment, such as a cross belt analyzer manufactured by Gamma-Metrics of USA, to find limestone composition at the conveyor belts, high-pressure twin roller press, and six-stage preheater.
The Technology with a modern control system comprises:
- A stacker and reclaimer.
- An online X-ray analyzer.
- A Fuzzy Logic kiln.
- Other process control.
It is essential to note that the cooling rate of the clinker considerably influences the strength properties of cement. The cooling rate affects the degree of crystallization, the size of the crystal, and the number of amorphous materials present in the clinker.
The properties of this amorphous material for a similar chemical composition will be different from the crystallized one. It is all about the manufacturing of cement.
One of the exciting points about cement is that the strength properties of cement depend on the cooling rate of the clinker as the cooling rate affects the degree of crystallization.
Disclaimer: The information on this website and blog is for general informational purposes only and is not professional advice. We make no guarantees of accuracy or completeness. We disclaim all liability for errors, omissions, or reliance on this content. Always consult a qualified professional for specific guidance.