What Is A Supplementary Cementitious Material?
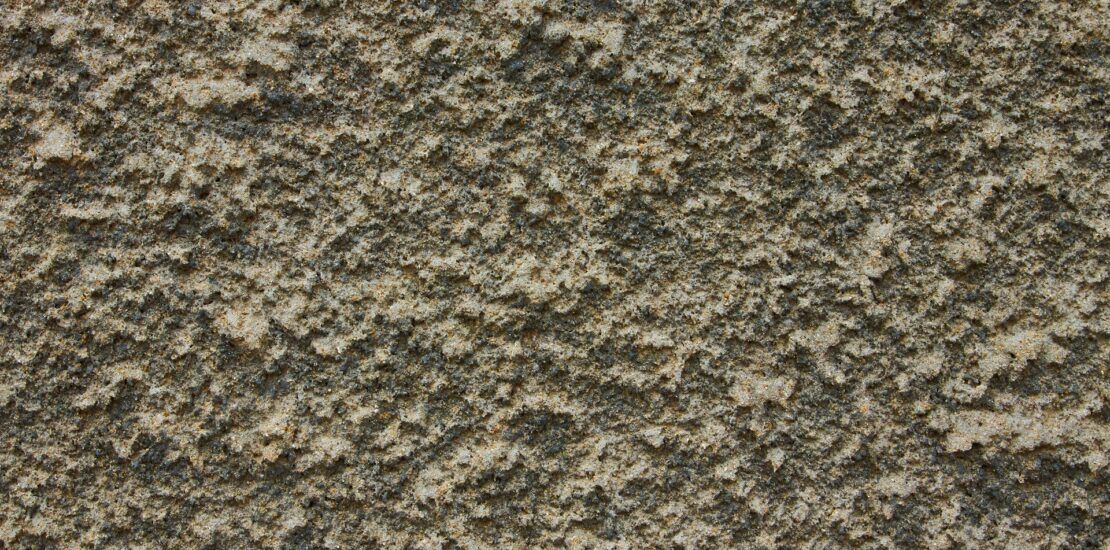
There is nothing called pure concrete. At best, it is a mixture of portland cement, coarse aggregates, sand, and water. Depending on what properties one desires of the final product, the mixture can vary in composition. Those materials added to the cement to change its properties are commonly referred to as the Supplementary Cementitious Materials. To make it easy to remember, these are the materials that supplement the cement to enhance or modify its properties.
Meaning Of Cementitious
The word Cementitious is used to describe a material with properties similar to that of cement or mortar.
What Is Supplementary Cementitious Material?
Supplementary Cementitious Materials are also known as SCMs. Another phrase that is used for them is “Mineral Admixtures.” These materials or substances are used in combination with Portland cement or blended cement. They add to the properties of hardened concrete through hydraulic or pozzolanic activity. SCMs are used as partial cement replacements to:
1. Lower costs
2. Improve the properties of the final product (mortar, concrete, etc.) in regard to durability.
An essential thing to bear in mind about Supplementary Cementitious Materials is that they have to meet the requirements of established standards. Based on their conformity to the standard specifications, they are added in different percentages to cement.
Types Of SCM
Traditionally, based on their origin, the Supplementary Cementitious Materials are classified under 2 main heads:
1. Natural Pozzolan
s – Other than grinding, these pozzolans require no further processing. Examples of natural pozzolans are limestone, clays, pumice, opaline rock, etc.
2. Artificial Pozzolans
– These result from chemical or structural modifications to substances with weak or no pozzolanic activity. They are sourced from industrial waste or selected raw materials. Examples of artificial pozzolans are marble powder, furnace slag, fly ash, burnt shale, glass powder, silica fume, etc.
Advantages Of Using Supplementary Cementitious Materials
1. Improve Performance – SCMs are used for enhancing the performance of concrete in its fresh or hardened state. The prime objective of using them is to make the end product workable, durable, and strong. Using SCMs, the concrete producers can modify the mixture to suit their purpose and achieve the desired result.
2. Stable Construction – Concrete mixtures with a high Portland cement content are prone to generating more heat and developing cracks. So, the result will not be a smooth finish. Rather, it will be a broken and uneven surface, which will render the stability of the construction also questionable. Nevertheless, these occurrences can be controlled to some extent by adding Supplementary Cementitious Materials to the mix.
3. Constructive Use Of Byproducts – SCMs like silica fume, fly ash, and slag allows the cement industry to use millions of tons of byproduct materials that would otherwise have been a waste and probably gone into a landfill.
4. Greener Impact By Reducing Consumption Of Portland Cement – The production of Portland cement is generally associated with high energy consumption and emissions. Therefore, anything that reduces its demand is considered a green initiative. Adding SCMs reduces the consumption of Portland cement per unit volume of concrete, and hence, its use is an environment-friendly concept.
Disadvantages Of Using Supplementary Cementitious Materials
1. Increases The Setting Time – Adding SCMs increases the setting time of concrete, which means it will now take longer for the mix to set and dry. Therefore, you need to revise the construction timelines and account for the additional time it will take for the concrete to be set completely.
2. Adds To The Cost Where SCMs Are Not Available Easily – Many countries do not have adequate quantities of SCMs, natural or otherwise, to meet their construction demands. The only option they have is to import more and store it in large quantities if they wish to avoid supply chain issues. This adds to the expense as you will need someplace to stock the materials and also pay for its handling.
3. Makes It Difficult To Change The Mix Design – As repeatedly pointed out, the addition of SCMs changes the properties of concrete. The disadvantage is that there is no flexibility to change the mix design with any ongoing construction project. Doing so will bring about visible differences in the appearance and quality of construction.
Commonly Used SCMs
1. Fly Ash – The most commonly used pozzolan in concrete is fly ash. Commercially, it is available as a fine residue resulting from the combustion of coal (in thermal power plants) and is transported from the furnace’s combustion chamber by the exhaust gasses. Depending on the concrete’s performance requirement, the fly ash content can be anywhere between 5% to 65% by mass of the cementitious materials.
2. Slag – Slag is sometimes also referred to as Ground Granulated Blast Furnace Slag (GGBFS). It is a glass-like, granular substance that results from the rapid chilling of molten iron blast furnace slag. Typically, slag has cementitious properties, but these become even better when used in conjunction with Portland cement. Its quantity ranges between 20% to 70% by mass of the cementitious materials.
3. Silica Fume – Sometimes, Silica fume is also called micro-silica or condensed silica fume. It is a highly reactive pozzolan, a byproduct of silicon or ferro silicon metal manufacturing. Silica fume is a very fine powder almost 100x smaller than the average grain of cement. It is used between 5% to 12% by mass of cementitious materials in constructions that demand reduced permeability to water and high strength.
To Sum Up
Supplementary Cementitious Materials or SCMs are partial cement replacements that improve the performance and properties of the end product, particularly in respect of its durability. There is no optimum combination of SCMs. It varies based on what the construction demands. Usually, the ready-mix concrete producers use their knowledge of the SCMs available locally to blend cement and meet the performance requirement. Today, using SCMs serves gains on multiple fronts. It reduces wastage and puts several byproducts to good use. Moreover, it reduces the need for cement in any construction project without raising concerns about the durability of the finished project. Yes, it may have some concerns of added costs and longer setting times, but that is a small price to pay in the bigger picture of things.
Disclaimer: The information on this website and blog is for general informational purposes only and is not professional advice. We make no guarantees of accuracy or completeness. We disclaim all liability for errors, omissions, or reliance on this content. Always consult a qualified professional for specific guidance.