What Are The Uses Of Cement Clinker?
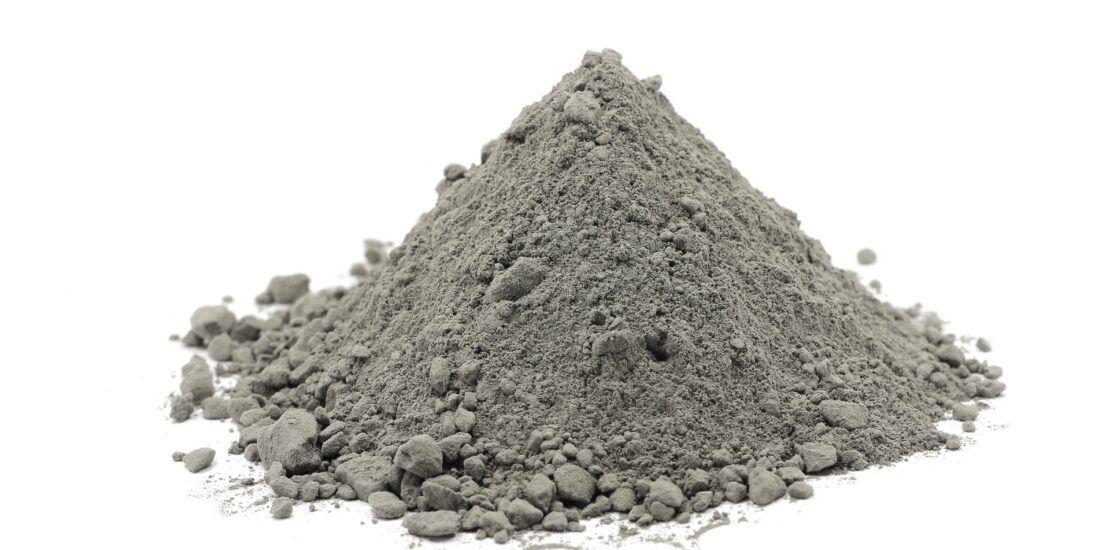
Clinker is a crucial product for making cement. Without it, most constructions would come to a standstill. Hence, it is also referred to as the very “backbone” of the cement industry. If you wish to learn more about clinker and its uses, you are on just the right page.
Clinker
When limestone and minerals are heated (to the point of liquefaction) in a kiln, a transformation process takes place in which carbon dioxide is released, and a small nodular mass is formed. These nodule lumps are called clinkers. They are approximately 3 mm to 25 mm in diameter and dark gray in color.
Clinker is a dry, hardened mass and, therefore, can be stored for long periods without any degradation in its quality. As a result, it makes for easy trading and storage.
Main Components Of Clinker
Typically, clinker has 4 main components. These are:
- Alite – Tricalcium silicate, Ca₃SiO₅ (in oxide terms 3CaO.SiO₂), abbreviated to C₃S. It is around 65% of the total.
- Belite – Calcium silicate, Ca₂SiO₄ (in oxide terms 2CaO.SiO₂), abbreviated to C₂S. It is around 15% of the total.
- Ferrite – Tetracalcium alumino-ferrite, Ca₂AlFeO₅ (in oxide terms 4CaO.Al₂O₃. Fe₂O₃), abbreviated to C₄AF. It is about 8% of the total.
- Aluminate – Tricalcium aluminate, CaAl₂O₆ (in oxide terms 3CaO.SiO₃), abbreviated to C₃A. It is around 7% of the total.
Other than these four components, trace amounts of salt phases and low-temperature phases are also present.
Types Of Cement Clinker
The clinker type varies depending on the type of cement for which it is produced. Presently, the most common types of clinker are produced for Portland Cement and its different blends. Some special types of cement clinker are:
- Low Heat Clinker – This type of clinker comprises 29% alite, 54% belite, 15% ferrite, 2% aluminate, and very little free lime. The production of low heat clinker has now ceased because the cement made from ordinary clinker and ground granulated slag has similar excellent low heat properties.
- Low Alkali Clinker – Alkali content is the presence of sodium oxide (Na₂O) and potassium oxide (K₂O) in cement. An increase in the alkali content of cement delays setting, reduces the compressive strength, and increases chloride ion permeability. Low alkaline levels will have reverse effects. The alkali content in the clinker is reduced by installing an “Alkali Bleed” or by replacing the raw mix alumina source with some other component.
- Sulfate Resistant Clinker – This type of clinker contains 76% alite, 5% belite, 16% ferrite, 2% aluminate, and 1% free calcium oxide. In recent years, its production has significantly declined because sulfate resistance can be achieved even by using granulated blast furnace slag in the production of cement.
- White Clinker – The white clinker contains 76% alite, 15% belite, 7% aluminate, no ferrite, and only 2% free lime. The absence of ferrite gives it a white appearance, but this composition may still vary extensively.
- Belite Calcium Sulfoaluminate Ternesite (BCT) – This is more a concept that produces a type of clinker which is greener for the environment. It lowers the carbon dioxide emission by around 30% and helps save approximately 15% in electricity costs.
Hydration Of Clinker
When water is added, the minerals in the clinker react to form different hydrates and set them as a hydrated cement paste. The primary binding component of hardened cement paste is the calcium silicate hydrates. Even after the initial setting, the process of hardening continues, which increases the mechanical strength of the construction. The longer the curing time, the stronger the structure.
Uses Of Cement Clinker
- Cement Clinker, mixed with additives and pulverized into a fine powder, is used for binding purposes in cement products . Various elements are added to achieve explicit properties in the cement. For example, adding gypsum to crushed clinker regulates the curing time and gives the cement compressive strength.
- Additionally, the clinker prevents accumulation and layering of the powder on the surface of balls and the mill wall . A few organic substances, like Triethanolamine ethylene glycol, oleic acid, etc., are also added to aid the grinding process and avoid powder accumulation.
- White cement clinker is used for aesthetic reasons in constructions. It is even used for making sculptures, columns, artistic borders, etc. Most of the white cement clinker goes into making factory-made pre-cast concrete applications.
- Sometimes chemical admixtures are added to the clinker to make other types of cement . A few examples are silica fume cement, ground granulated blast furnace slag cement, and pozzolana cement.
- Portland cement clinker is also a basic component in making plaster, mortar, and non-specialty grout .
Advantages Of Clinker
- Adding clinker makes the concrete more resistant to shrinking and cracking.
- Its addition helps vary the drying and setting times per the construction demands. But in this case, having precise knowledge is paramount. Small-time project managers may lack this.
- Since clinker and subsequently the cement made from it is easy to transport and store, it makes for easy trading. One can even buy and store it without having to worry about quality deterioration. But of course, you need to ensure it is kept dried.
Disadvantages Of Clinker
- The varying curing times one can achieve with clinker are not always looked upon favorably by project managers. The reservations and discontent arise more from the fact that their own knowledge in this aspect of handling cement is pretty limited.
- Again, the lack of knowledge makes them more dependent on the ready-mix cement companies. So they are unable to make the cement on their own. Thankfully, buying ready-mix cement bags is easier and more affordable, making this drawback lose weight.
Bottomline
Clinker is the core product for making cement. On its own, it may not serve any purpose, but when mixed with gypsum and other additives, it increases the workability of cement and, consequently, the concrete. Therefore, the main use of clinker is in making different types of cement. It is also used in mortar, plaster, grouting, etc. However, critical in all this is knowing the proportions in which clinker needs to be mixed with other additives to get uniform and consistent results. Fortunately, with companies supplying ready mix cement bags, the lack of this knowledge does not lead to any dire consequences
Disclaimer: The information on this website and blog is for general informational purposes only and is not professional advice. We make no guarantees of accuracy or completeness. We disclaim all liability for errors, omissions, or reliance on this content. Always consult a qualified professional for specific guidance.