Unpacking the Various Components of Cement
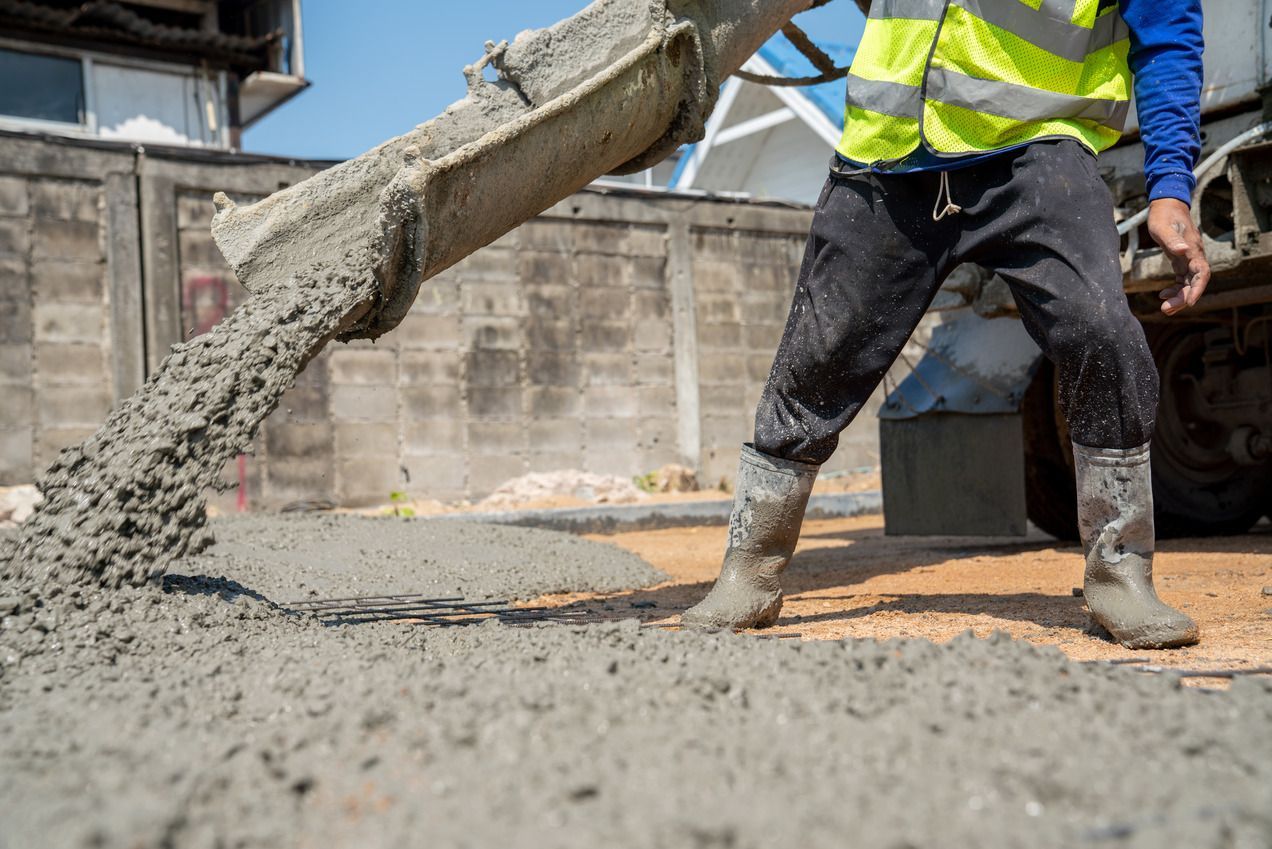
Cement might appear to be a simple grey powder, but don’t be fooled. It’s a carefully crafted substance that plays a critical role in construction, laying the foundation for structures that stand the test of time.
From skyscrapers to your own backyard patio, the utility of this material extends far and wide. Today, we’re examining the various components that go into creating quality cement. We’ll also be sharing the creation process. It’s a fundamentally simple process comprised of many complex facets. Intrigued? Let’s explore.
The Fundamentals of Cement
When talking about cement, you might think it’s just another component in the construction repertoire. However, the making of cement is a high-stakes, intricate process. Formulated from a mixture of calcium, silicon, aluminum, iron, and trace elements, this composition doesn’t happen by chance. Far from it.
You see, before a bag of cement even gets to the hardware store, it’s subjected to a gauntlet of quality control measures. Both chemical and physical tests are conducted rigorously to verify the material’s composition, strength, setting time, and a range of other properties.
Lime for Strength and Stability
When it comes to lime, which is either calcium oxide or calcium hydroxide, precision in quantity is critical in cement production. Lime is primarily responsible for forming calcium silicates and aluminates, the compounds that provide cement its strength.
The catch is that the amount of lime in the mix must be carefully controlled. Insufficient lime speeds up the setting time of the cement, compromising its strength. On the other hand, an excess amount of lime can lead to cement that is unstable and prone to disintegration.
Silica for Durability
Silica isn’t just an additive; it’s a cornerstone of the chemical makeup. Comprising approximately 30% of a typical cement mix, silica carries substantial weight in the composition. The influence of this component extends to forming essential compounds—namely, dicalcium and tricalcium silicate—that take the credit for the material’s durability.
But why is this even important? In the world of construction, durability is an absolute must. Buildings, bridges, and even sidewalks must withstand varying conditions, from the wear and tear of daily use to extreme weather patterns. That’s where silica steps in, ensuring that the cement used in these projects is up to the challenge.
Alumina
Alumina, also known as aluminum oxide with the chemical formula Al2O3, has a specific function in cement: it accelerates the setting time. This chemical component also reduces the clinkering temperature, which is the high temperature that raw materials reach to form clinker during the production of cement.
However, there’s a cautionary note. Too much alumina can have a weakening effect on the cement’s overall strength. Obviously, that would negate the overall function of cement. Thus, precision is necessary to ensure optimal performance.
Magnesia and Iron Oxide
Magnesia (MgO) holds a very specific yet crucial role in the chemistry of cement. To preserve the integrity and strength of the final product, it is important that magnesia constitutes less than 2% of the mixture. Any more than that, and you’re asking for trouble in terms of structural strength.
Iron oxide (Fe2O3) wears more than one hat in the cement-making process. First, it bestows upon cement its distinct hue, which can range from a sandy yellow to a deep red, depending on its concentration. Second, it acts as a flux during production.
What does that mean? Well, in layman’s terms, a flux helps facilitate chemical reactions during the production process, making it easier for raw materials to combine into the final product we recognize as cement.
Calcium Sulfate and Sulfur Trioxide
Think of Calcium Sulfate (CaSO4) as the responsible adult in the room when it comes to the chemistry of cement. Its primary role is to slow down the setting process, offering a balanced, controlled approach to hardening. It prevents the cement from setting too quickly, which could lead to structural problems down the line.
Sulfur Trioxide (SO3) joins Calcium Sulfate in this regulatory endeavor. However, precision is crucial; the proportion of SO3 must not exceed 2% in the mix. Going beyond this limit could result in unsound cement, which is as problematic as it sounds.
Alkaline Substances
In cement manufacturing, alkaline substances occupy a critical role that is often understated. While they may not be the star players in the chemical composition, they certainly are the gatekeepers of balance. A concentration of less than 1% is a standard upheld across the industry, ensuring that the cement achieves its necessary structural integrity, setting speed, and aesthetic uniformity.
Monitoring the alkaline concentration is a non-negotiable task. Why? Because surpassing the recommended 1% threshold opens the door to several complications. The most notorious among them is efflorescence—a phenomenon where unsightly, chalk-like deposits form on cement surfaces.
This not only affects the appearance but can also raise questions about the overall quality of the cement. The role of alkaline substances may seem minor, but maintaining their appropriate concentration levels is a must. Stray beyond that, and the drawbacks are immediate and visible, from aesthetic issues to questions of reliability.
The Making of Cement
Now that you know the compounds and components that make up cement, it’s time to turn our attention to how they come together to create the formidable substance. It’s not merely a matter of mixing things together. Cement production requires careful steps to get the end result. Let’s observe:
1. The Grinding Stage
Once the raw materials have been collected, they’re off to be crushed and ground into a fine powder. This isn’t your everyday mixer; specialized industrial grinding equipment is used for this step. The outcome is a homogeneous mix that’s ready for the heat—quite literally.
2. Into the Kiln
The ground materials now enter the rotary kiln, an essential apparatus that heats them to temperatures north of 2,700°F. Think of it as the furnace of creation for cement. The high heat triggers a series of chemical reactions that lead to the formation of ‘clinker,’ small lumps that are the precursors to cement.
3. Clinker to Cement: The Final Stretch
After leaving the kiln, the clinker is rapidly cooled and then subjected to yet another grinding process. At this stage, a few more components like gypsum are added to the mix. This final grinding step is essential to achieving the desired properties of cement, whether it be quick-setting or long-lasting durability.
Quality Control: A Non-Negotiable Step
Before it gets the seal of approval, the cement undergoes a series of tests. These range from chemical analyses to determine the composition to physical tests that measure attributes like setting time and strength.
Any variations from industry standards are unacceptable; the cement must pass every test to make its way to construction sites. So by the time cement reaches its final destination, it’s a highly engineered product designed for strength, durability, and adaptability.
Wrap Up
Cement is a marvel of engineering, touched by meticulous quality control measures and formulated to meet precise specifications. From small DIY projects to complex infrastructure, cement is ever-present in our constructed environment.
Disclaimer: The information on this website and blog is for general informational purposes only and is not professional advice. We make no guarantees of accuracy or completeness. We disclaim all liability for errors, omissions, or reliance on this content. Always consult a qualified professional for specific guidance.