How to Use Calcium Aluminate Cement in Refractory Applications
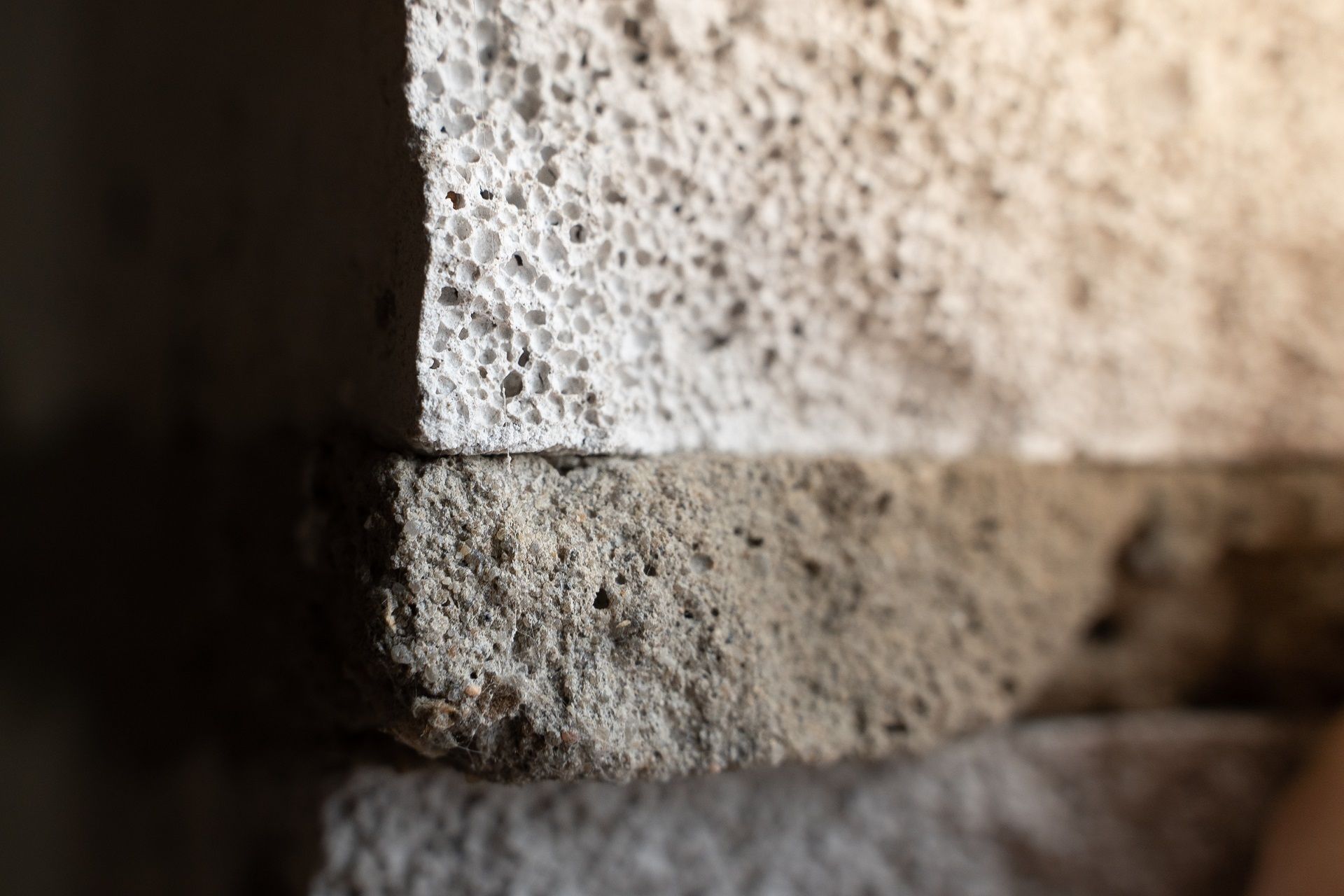
Are you looking for a powerful refractory material? Then look no further than calcium aluminate cement! This versatile, heat-resistant material is perfect if you need to work with high temperatures. Plus, it makes the job easier and faster too. So let’s learn more about this amazing stuff and how to use it in your refractory applications. Ready to get started? Let’s dive in!
Properties of Calcium Aluminate Cement
Before we jump into the applications of calcium aluminate cement, let’s take a minute to learn about its composition and properties. We can break this down into three categories: composition and chemical properties, physical properties, and mechanical properties.
Composition-wise, calcium aluminate cement is typically composed of 45-50% calcium oxide and 40-45% aluminum oxide. It also contains small amounts of silica, magnesia, and iron oxide. As for its chemical properties, this material has excellent corrosion resistance, high acidity levels, and a low water absorption rate.
Physically speaking, calcium aluminate cement is white in color but turns gray when it comes into contact with water. It also has a high degree of thermal expansion (which helps to reduce cracking) and low sound transmission.
Finally, when it comes to mechanical properties, calcium aluminate cement boasts excellent compressive strength and good resistance to wear and tear.
Applications of Calcium Aluminate Cement in the Refractory Industry
Now that we’ve taken a look at the composition and properties of calcium aluminate cement, it’s time to talk about its applications in the refractory industry. So why is this material such a great choice for these types of projects?
Well, one of the main reasons is its heat-resistant properties. This makes it perfect for applications where high temperatures are involved, such as steel furnaces or blast furnaces.
Plus, its low water absorption rate also makes it a great choice for jobs that involve direct contact with hot liquid materials like slags, flue gases, and slurry. Finally, calcium aluminate cement can also be used to create shapes that are difficult to achieve with other materials.
Mixing and Installation of Calcium Aluminate Cement
Now that we’ve discussed the applications of calcium aluminate cement, let’s go over how to mix and install it properly. Firstly, when mixing cement for refractory applications, be sure to use clean
water and a power mixer. This will ensure that the cement is evenly distributed and all of its components are thoroughly mixed.
Once your mixture is ready, it’s time to start installation! While the exact process may vary depending on the application, there are some general guidelines you should keep in mind. For instance, be sure to use a stainless steel trowel for even application and avoid any wet or dry spots.
Also, keep in mind that calcium aluminate cement takes longer to cure than other materials — usually two days at least! So be sure to factor this into your project timeline.
Maintenance and Repair of Refractory Linings
When it comes to refractory linings, maintenance and repair are necessary from time to time. For instance, regular inspections can help you identify weak points before they become a major issue. Plus, it’s also important to make sure the lining is completely dry before applying repairs.
Repairs themselves typically involve patching up damaged areas or filling in gaps with mortar or grout (usually made from calcium aluminate cement). If you’re not sure how to proceed, it’s always best to consult a professional.
Safety Considerations
Finally, we want to talk about safety considerations when using calcium aluminate cement for refractory applications. As with any construction project, proper protective gear should always be worn and certain tools should not be used without proper training. Additionally, it’s also important to make sure that the area is well-ventilated and all containers are labeled correctly.
By following these simple guidelines, you can ensure that all of your refractory projects go as smoothly as possible!
There you have it — everything you need to know about using calcium aluminate cement in your refractory applications. From its composition and thermal properties to installation and maintenance, this material is sure to make any project easier. And with the right safety precautions in place, you can rest assured that your work will be completed safely and efficiently!
So what are you waiting for? Get started on your next refractory project today!
Common Materials Used with Calcium Aluminate Cement
Now that you know how to use
calcium aluminate cement in refractory applications, let’s take a look at some of the materials commonly used alongside it.
One of the most popular choices is fireclay, which is often used to create a protective layer on top of calcium aluminate cement mixtures. Fireclays also help increase thermal protection and improve the overall strength of your lining.
Another material frequently used with this type of cement is insulating castables. This gives your project an extra layer of insulation against heat, ensuring better performance and longevity. Additionally, insulating castables are easy to install and require minimal maintenance, making them an ideal choice for those short on time or resources.
Finally, there are also a variety of sealants and adhesives that can be used to improve the strength and durability of your refractory lining. These include masonry cement, asphalt emulsion, and even epoxy-based products. By using these in combination with calcium aluminate cement, you can create a truly durable yet flexible system that will stand up to any challenge!
Wrap Up
Using calcium aluminate cement in your refractory applications is an excellent choice thanks to its heat-resistant properties, low water absorption rate, high compressive strength, and ability to create complex shapes with ease.
When mixing or installing it, be sure to use clean water and a power mixer plus follow all safety guidelines. Finally, regular inspections of refractory linings are absolutely essential for identifying weak points and making necessary repairs.
By following these tips, you can be sure that all of your refractory projects will be completed safely and efficiently!
Need Raw Materials for Your Next Project? Call PermuTrade!
At
PermuTrade, we offer a variety of raw materials to meet your needs. Whether you’re looking for calcium aluminate cement or something else, we have the products you need and the expertise to help you get the most out of them.
Contact us today via our
contact form to learn more about how we can help with your next refractory project!
Disclaimer: The information on this website and blog is for general informational purposes only and is not professional advice. We make no guarantees of accuracy or completeness. We disclaim all liability for errors, omissions, or reliance on this content. Always consult a qualified professional for specific guidance.